July 1, 2019
The IMechE UAS Challenge is a yearly challenge that consists of a simulated humanitarian aid mission. An example of such a rescue mission is delivering first aid, water and food to survivors in an area hit by earthquakes. Teams of Undergraduate and taught Postgraduate students from international universities compete in the designing, constructing, developing and demonstrating an Autonomous UAS (Unmanned Aircraft System). The system is required to operate autonomously, performing a series of tasks such as area search, navigating waypoints, accurately dropping Aid Packages and returning to base via a defined route. The key challenges involved are autonomy, optimising the configuration and structure of the UAV for the mission, and designing an accurate payload delivery system.
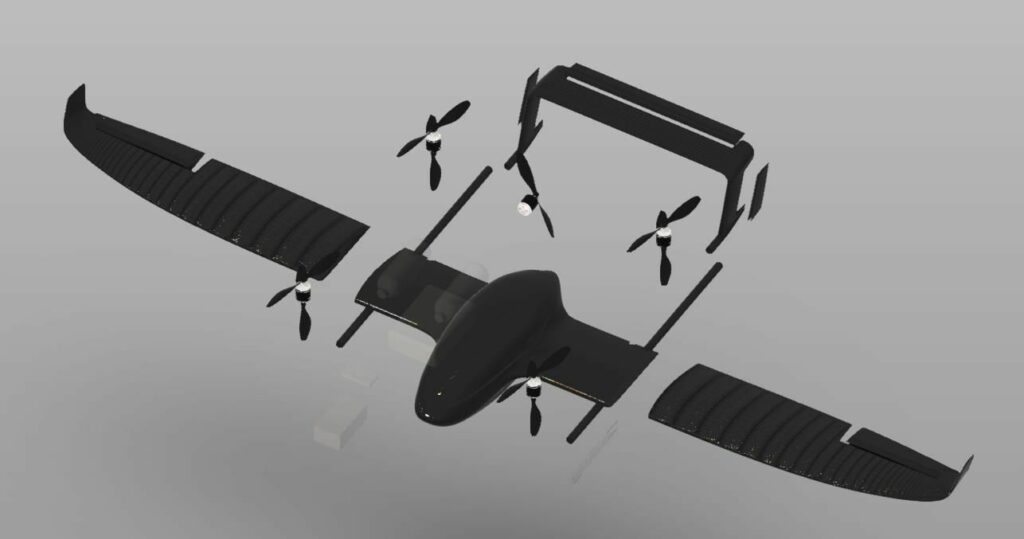
After performing trade studies, the team settled on a Vertical Take-Off and Landing (VTOL) – Plane configuration that required a lot of optimising in energy and power consumption. The droneteam’s engineers have simulated the power consumption over time for different specifications of components and settled on an octa-plane configuration, which means 8 motors are used for VTOL and one for a forward motion. Since these VTOL motors were required for only ~5% of the mission flight time, we traded the power-energy costs for weight reduction. The total power consumption of the UAV in VTOL is about 2.5 kW as compared to about 500 W in plane mode. The VTOL motors weigh only 50g each with the propeller, putting the total VTOL weight cost at 400g. Since the aircraft is 5 times more efficient in plane mode, it has enough battery capacity to complete the required mission flight times.
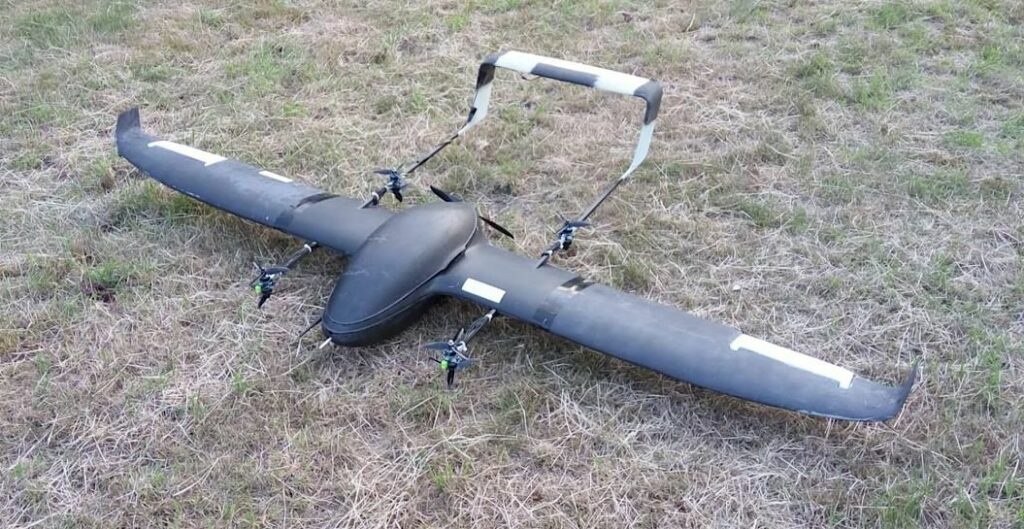
Because the optimising of the structure was so important, another big challenge is the building of a high-quality frame. A lot of different materials can be used for the frame of a UAS. We wanted to use the lightest and strongest material available, carbon fibre. Unfortunately, although carbon fibre is a great material, it is quite expensive. Fortunately our partner Fiberneering provided us with their in-house developed FRP3D (3D printed composites). This method is able to combine a 3D printed substructure and the carbon fibre into one, giving us the ability to build the frame of the drone in a cheap and efficient way. The freedom of the 3D-printing gave us all the possibilities in designing the frame, as can be seen in the images.
We are looking forward to flying our drone at the UAS Challenge, and hope to achieve a good result.